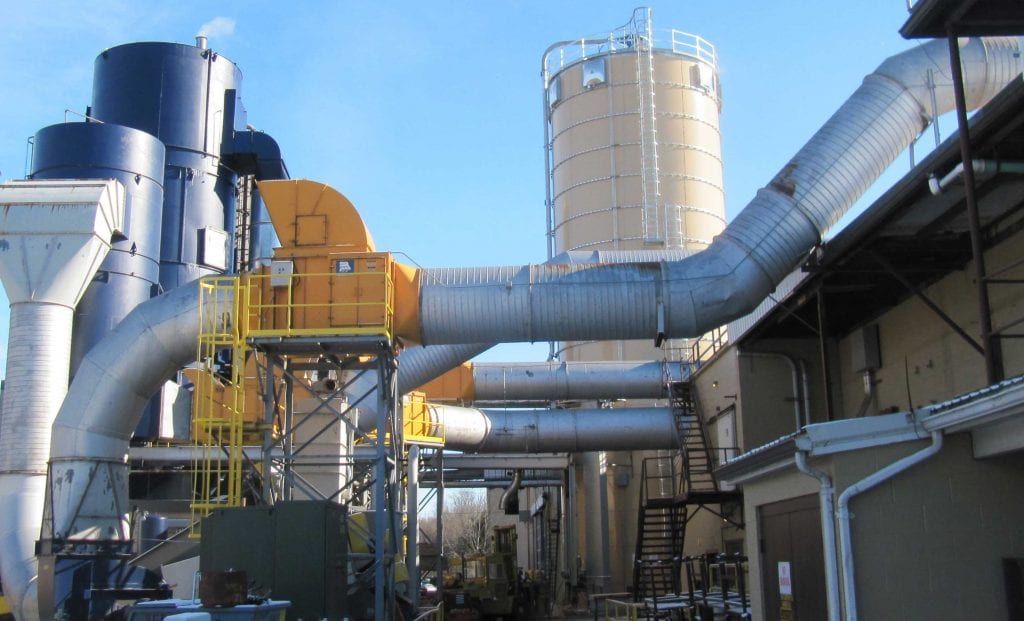
Pressure relief system panels around the top of a silo can help alleviate pressure and avoid combustible dust explosions.
Published in the November 2019 issue of Powder and Bulk Engineering
Combustible dust hazards exist in many bulk solids industries, and a dust hazards analysis can help you pinpoint potential trouble spots. This article first describes the basics of conducting a dust hazards analysis and then explains storage tank venting system options that can be used to mitigate those hazards.
Keith McGuire, CST Industries, Inc. and Brian Edwards, Conversion Technology, Inc
Any combustible bulk solid — and even some normally non-combustible solids when reduced into small enough particles — can cause an explosion when certain concentrations and conditions occur. When small material particles are in suspension the material tends to burn (oxidize) very quickly.
There are five factors needed for a combustible dust deflagration or flash-fire to occur: fuel (combustible dust), oxygen (typically in the air), an ignition source (heat), confinement, and dust dispersing into a cloud. If all these factors come together in a contained area, and the building, storage tank, or compartment doesn’t have the strength to contain the resulting pressure, a combustible dust explosion can occur.
For dust to become explosive, it requires a concentration at or above its minimum explosible concentration (MEC), which is the minimum amount of dust that will explode when dispersed in air. These concentration levels can accumulate in process equipment such as bins, storage tanks, conveyors, air–material separators (cyclones, baghouses, bin vents), ductwork, and other spaces. With all five factors present, the dust can ignite in the confined space, causing a relatively minor explosion. This disturbs and disperses the accumulated dust, creating a dangerous dust concentration in that space. The first fire acts as the ignition source for a secondary explosion, which uses the dispersed dust for fuel, and often can be much larger and more destructive than the initial deflagration.
Conducting a DHA
The severity of the hazards present in a facility are influenced by a number of factors. These include the nature and quantity of dust, the equipment configuration, the equipment’s materials of construction, the facility layout, the existence of ignition sources, and the proximity of the hazards to employees and other structures. A dust hazards analysis (DHA) is a systematic analytical study of a given facility and its components and processes to identify potential combustible dust hazards. Conducting one can help you identify and mitigate trouble spots.
Specifically, NFPA 652: Standard on the Fundamentals of Combustible Dust, requires that a DHA include the following:
• Identification and evaluation of locations or processes throughout the facility where potential fire, flash-fire, or explosion hazards exist.
• Identification and evaluation of specific fire and deflagration scenarios where these hazards exist.
• Identification of safe operating ranges of processes and equipment, such as flow rates, temperatures, etc.
• Identification of any safeguards that are in place to mitigate the fire or explosion hazards.
• Recommendations for additional safeguards where needed
In a DHA, a detailed review of each process component and building or area where combustible dust is handled, generated, or present is conducted.
The first step is to identify the components and areas to be included in the DHA. This can be done by reviewing process and facility drawings and by touring the facility. For each component and area included in the DHA, the person conducting the analysis must determine the potential for a hazardous atmosphere to be present and identify operating conditions that could result in a hazardous atmosphere. These should include normal operating conditions, start-up/shut-down conditions, and potential upset conditions.
Next, all potential ignition sources should be identified for each process component. Potential ignition sources can include open flames, electric devices, static electricity, mechanical impact and friction, hot surfaces, hot work, powered industrial trucks, and others. Based on the configuration, design, and interconnectivity of an area or process component, deflagration and explosion scenarios and their impact should be identified.
The next DHA step is to identify any current safeguards — explosion protection, deflagration isolation, ignition source control, dust control, housekeeping — in place to mitigate combustible dust hazards.
Once all this data has been compiled, a risk characterization should be conducted. If the risk characterization finds that the risk level isn’t acceptable, recommendations for additional risk-reducing safeguards need to be provided.
Mitigating storage equipment hazards
The DHA must be completed or led by what NFPA standards define as a qualified person who has demonstrated the ability to understand combustible dust and its associated hazards through education or experience.” i.e., someone knowledgeable of the science of dust fires and explosions as well as the specific hazards of the process being reviewed.
If the qualified person determines that your process equipment requires additional safeguards to reduce the risk, there are mitigation options. According to Dr. Chris Cloney, director of DustEx Research, a consulting company that focuses on combustible dust safety, 37 percent of deflagration events occur when conveying bulk solid materials to storage and in storage tanks, and 24 percent occur in bin vents.
Evaluating the stored material’s specific properties is important when determining the potential severity of a tank, vessel, or bin vent deflagration. This includes understanding the material’s specific nature and properties, including factors like Kst (deflagration index for dust) and Pmax (deflagration pressure). Using these two factors, along with the principles of NFPA 68: Standard on Explosion Protection by Deflagration Venting, a qualified engineer can calculate Pred (maximum pressure developed during venting). With this information, a silo can be designed with enough strength to safely operate during an overpressure event. This likely will require incorporating one of two common pressure venting relief systems into the storage equipment to provide explosion protection.
The first venting system involves explosion panels, which are independent relief devices located in the air space or head space of a tank and designed to burst at a determined pressure. Using NFPA 68 equations and given the Pstat (vent release pressure), you can determine the quantity and size of explosion panels needed. These devices also can be installed on bin vents or other equipment where emergency venting may be necessary. Note: Make sure the explosion panels are oriented away from any staff access areas or other system components.
The second venting system is a weak-seam deck, also referred to as a frangible roof, where the roof-to-shell joint or connection is designed to separate and release pressure through the top of the tank. When using this system, consideration must be made to be sure that no other weight or restrictions are added to the top of the deck that may limit its proper operation.
Both types of systems have their benefits and limitations depending on the application, the process equipment location, the physical layout and constraints of the tank, the building, and the surrounding areas.
Other possible modifications
Once the type and specifics of the pressure relief system have been determined, they can be incorporated into a tank’s design. This can be done relatively easily for new tanks and facilities but can become more difficult when retrofitting an existing tank or process equipment. There are many factors to consider in this situation; primarily, what is the required operating volume?
If there’s sufficient storage capacity, the quickest and easiest method is to install the explosion panels directly into the existing tank shell. This can be done by field-cutting openings in the tank shell and installing the requisite frame to connect the explosion panels. The material storage level must remain below the explosion panels, so if the panels are placed in the top of the tank shell, the effective storage volume will likely be reduced. Depending on the physical characteristics of the environment, several options exist to maintain the volume.
• The existing tank may be modified by removing the upper portions of the tank and replace them with new explosion panels pre-installed in a new tank shell including a new roof. If the present tank volume needs to be maintained, the tank height must be increased to accommodate keeping the product below the explosion panels. The condition and design of the tank requires evaluation prior to any structural and deflagration venting modification.
• Second, placing explosion panels in the tank’s roof may be possible. This depends on venting proximity to a safe environment, personnel access on and around the top of the tank area, and enough space in the roof to locate the panels.
In some instances, modifying the tank by raising it to allow for outside venting through the building structure or envelope might be possible, or ductwork could possibly facilitate safely exhausting the pressure outdoors. Other considerations may include adding stiffening or other reinforcement to the tank to resist the venting pressures.
Remember, when dealing with explosive dusts in your equipment and facility, consulting with qualified professionals and experts who have the knowledge and industry experience to identify and implement specific solutions is important.
About the Author
Keith McGuire, PE, is the structural engineering director for CST Industries, specializing in the design and fabrication of bolted and welded storage tanks, silos, and accessories. He graduated from Pittsburg State University with a degree specializing in structural, mechanical, and civil engineering and is active in numerous industry standards committees including API, AWWA, ASME, and NFPA.
Brian Edwards, PE, is the director of engineering for Norcross, GA-based Conversion Technology. He has a degree in civil and environmental engineering from Georgia Tech and has more than 20 years of experience as a consultant to industry. He has worked on various NFPA committees, including being a principal member on the committee for NFPA 61.