Published in the June 2019 issue of International Fire Protection Magazine
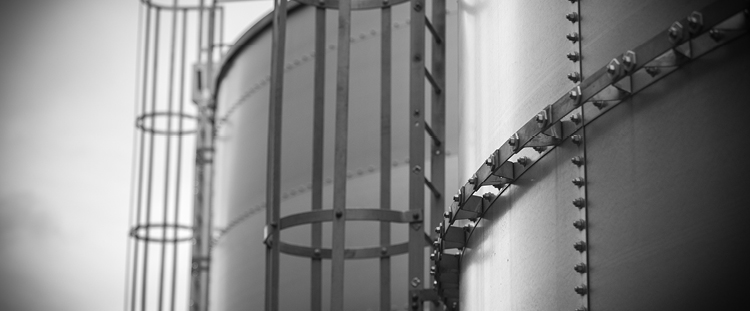
With over 350,000 field proven storage tank installations in more than 125 countries and a diverse product portfolio that now includes pre-configured tanks, CST understands the benefits bolted tanks can offer and how pre-configured tanks can provide the best value in the shortest lead time.
Why are design specifications important?
Well written specifications ensure the customer receives a quality product that meets the requirements of the job, meet code and ensure all bidders adhere to the minimum requirements. This enables the purchaser to review bids that are as near equivalent as possible. It can also help to identify where bidders have made an exception to the specification that can be discussed in further detail.
Specific to storage tanks, the specifications that will have the largest impact on the tank design are the product being stored, including the specific gravity or density, followed by the maximum wind speed and the seismic zone for the region where the tank will be located. The design code will not only help determine the maximum design wind speed and seismic criteria that should be used in the design, but also determine how the loads are applied to the tank and the safety factors required.
To determine the proper design code, the storage application and applicable codes for the country where the tank will be constructed should be reviewed. Design codes that are most common for bolted storage tanks include AWWA D103, FM 4020, API 12B, and Eurocodes. If considering a pre-configured tank, check to make sure that the design code and storage application are compatible with the available tank designs. Normally, pre-configured tanks will target a market and specific storage application where the design codes are consistent and have the most overlap between countries. For this reason, it is important to understand the target market when considering preconfigured tanks.
Variety of sizes and appurtenances
Once the applicable design specifications have been determined, the storage volume, followed by the optimal diameter and height should be considered. If there are no constraints limiting available ground space, then being flexible with the tank dimensions will maximize the options and minimize the cost. A larger diameter and shorter height will generally reduce the price of the tank, but this price savings can be somewhat offset by the roof and floor, so it is important to consider alternatives.
Bolted storage tanks come with a wide variety of options, starting with the floor and roof. Floors are typically steel or concrete. In many applications (low seismic and good soil) concrete is usually the most economical choice, but steel can reduce the foundation cost in high seismic areas or regions with poor soil. Steel floors are also preferred for hazardous applications where the risk of leaks must be minimized. Typical roofs include trough deck, low profile, column supported, and aluminum domes. Trough deck roofs are the most economical, but if a sealed roof is required, a low-profile roof is a good option. Aluminum domes are ideal if minimal maintenance is preferred. When considering pre-configured tanks, the sizes of available tanks and roofs will be optimized to provide the best price in the shortest lead time and a customer that remains flexible will be best suited to take advantage.
Finally, appurtenances such as ladders, manways, level indicators, pipe brackets and nozzles should be selected. While options may be limited when it comes to appurtenances offered with pre-configured tanks, the appurtenances offered are focused on the needs of the specific storage application and market. If possible, being flexible with appurtenances will most likely lead to an optimal solution with the best lead time and price.
Why are coatings so important?
If properly specified, coatings improve the life cycle and value proposition of the storage tank; balancing price and economy for longevity and minimizing downtime. Not only is the coating important to consider, but the coating process can have a significant impact on the quality of the coating. Bolted tanks, whether pre-configured or custom designed, are factory coated in a controlled environment with state-of-the-art automation and the most stringent quality control processes. At a minimum, a bolted tank supplier should test the surface preparation, inspect for holidays, check adhesion, measure thickness, and confirm the color as part of the coating process. Additional quality assurance measures such as verification of the oven temperature and line speed are also commonly implemented.
Common coatings for bolted tanks include galvanizing, both liquid and powder epoxy, and porcelain enamel (aka glass-fused-to-steel). Within each coating type, there are several tiers that offer higher quality, and it is important to understand the coating that a specific storage application requires. Variables that can determine the best coating type for a specific storage application include storage temperature, pH levels, and any additives such as fats, oils and greases.
A supplier that can offer various coating types and tiers within each coating type is most likely to be able to provide the best product for a given application.
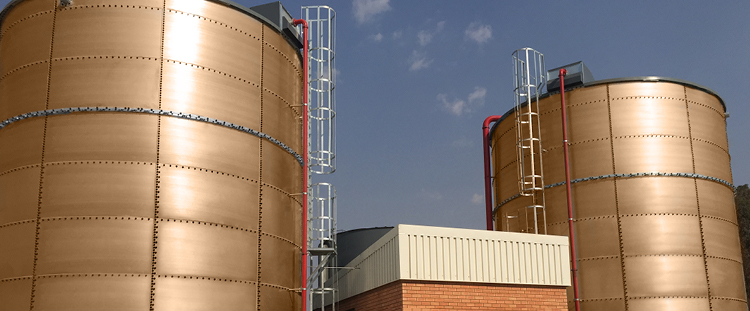
Not all tanks are the same
The type of storage tank and the method of construction should be carefully considered. Field welded, concrete, and bolted steel tanks are the most common types of storage tanks. While field welded and concrete share a large percentage of the global market, both have significant disadvantages when compared to bolted. Field welded tanks require skilled construction labor and specialized equipment; and have long construction lead times. They are also more susceptible to construction delays caused by weather and quality control issues due to weld testing and the field applied coating in a non-controlled environment leading to re-coatings and additional downtime.
In addition to some of the same challenges as field welded, concrete tanks are susceptible to hairline cracks that can leak, and biofilm growth due to the rough surface texture. With concrete tanks, some design standards allow a daily leakage limit of up to 0.5% due to the permeable / porous nature of concrete. Whether field welded or concrete, there are limited options for accelerated lead times through pre-configured tanks as the lead time is largely driven by the need for skilled labor and specialized equipment, in addition to engineering.
Bolted tanks not only offer shorter lead times and a superior coating but provide the most flexibility as the customer has the option to choose the method of construction that is best suited for the location and preference. Bolted tanks can either be designed as flat panel or API chime panel. Flat panel tanks are typically constructed from top-down with the use of construction jacks that allow crews to perform the bulk of the work at ground level. API chime tanks are scaffold-built from the bottom-up, eliminating the need for jacks. Other differences include how the bolted joints are sealed, API chime tanks use gaskets at the bolt seams, while flat panel tanks typically use sealant applied at the seams. The sealant type and gasket material can be changed to best suit the application. Both styles of bolted tanks have their advantages, depending on the tank size and resources available. Either type of bolted tank is suitable for pre-configured tanks, but the type and method of construction offered will be chosen based on the preferences of the target market.
Economical solution
Pre-configured bolted tanks can provide all the advantages of bolted tanks with additional advantages. Pre-configured designs allow the tank manufacturer to better anticipate inventory requirements and eliminate the need for custom engineering, allowing the manufacturer to share the benefits of cost savings with the end user. Pre-configured designs are best applied where there is less variability in what the market needs and the end user can remain flexible to take full advantage. Water storage applications such as municipal water, fire protection, and potable water, among others, are ideal uses for pre-configured tanks as these markets provide the most overlap in the requirements of the customers.
Delivery time
One of the primary advantages of bolted tanks is the lead time. Bolted tank manufacturers can offer significantly reduced lead times due to the advantages offered by manufacturing and coating the sheets in a controlled environment, without sacrificing quality. The sheets and tank components arrive on site ready to assemble without the need to pre-fabricate. Bolted assembly does not require skilled labor or specialized equipment, reducing the overall project timeline with a shorter construction lead time and less on-site costs. Bolted tanks can be engineered, delivered, and constructed within four months from time of order. Pre-configured bolted tanks can be delivered and constructed in 3 months from time of order by eliminating the need for custom engineering.
Are they competitive in lifespan?
Bolted steel tanks are just like field welded steel tanks, or any other steel structure, if properly maintained, they can seemingly last forever. However, if not maintained, factory coated bolted tanks will typically last longer than field welded due to the quality of the factory applied coating over a field applied coating. In addition, bolted tanks are easier to repair and upgrade when compared to field welded tanks or concrete tanks. For example, if there is sheet with coating damage, the bad sheet can simply be replaced with a new sheet that has been coated in a factory setting, eliminating the need to cut, fabricate, and weld a patch or develop any other type of expensive field fix. It is also common for flat panel, jack constructed tanks to be expanded by adding rows, providing the option to increase the tank volume as demand for storage increases.
Where should I start?
If you are in the market for a bolted storage tank, we hope that you find this information useful and will consider a pre-configured tank as we have found that they offer the optimal balance between quality, lead time, and price for most water storage applications. If you need a custom tank, CST has the largest product offering and options in the market, including premium epoxy and glass coatings.
For more information on Vulcan by CST storage systems call +1 844-44-TANKs or email sales@cstindustries.com
CST Contact Information:
CST Industries, Inc.
Kim Mathis
Global Marketing Director
713-351-3769
kmathis@cstindustries.com
CST Industries, Inc.
Aaron Johnson, P.E.
Director of Mechanical Engineering & New Product Development
913-428-7158
ajohnson@cstindustries.com